Rolling bearings, generally also often just called ball bearings, are used to fix shafts and axles. They transmit forces and moments depending on the design.
A rolling bearing usually consists of an outer ring (1), inner ring (2), the rolling elements (3) (balls, cylindrical rollers, needle rollers, tapered rollers or barrel rollers) and seals. The lubricant used in the rolling bearing is matched to the specific application. The rolling elements are generally separated from each other by a cage to produce uniform load distribution across the rolling elements.
There are five basic types of rolling bearings. Each type has special characteristics and is therefore particularly suitable for certain bearing arrangements:
In addition, influencing factors, for example, speeds, temperature, lubrication, vibrations or installation and maintenance must be taken into account when selecting the rolling bearing design.
Rolling bearings for predominantly radial loads are called radial bearings. Deep groove ball bearings or angular contact ball bearings can also support combined loads.
Not suitable for axial loads are, among others, cylindrical roller bearings, most needle roller bearings, drawn cup needle roller and cage assemblies.
Rolling bearings that are subjected to predominantly axial loads are referred to as thrust bearings.
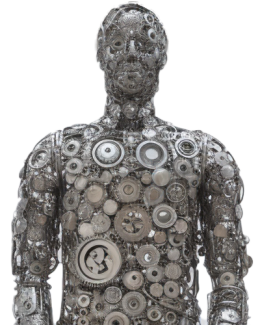
Your contact person
-
Roller bearings sales
-
+49 (2053) 497 - 36
-
Roler bearings
-
+49 (2053) 497 - 0
-
Opening hoursMo-Do.: 08:00 - 16:00
Fr.: 08:00 - 14:45
-
Delivery timesMo-Do.: 06:00 - 13:30
Fr.: 06:00 - 11:00
oder nach Absprache