The selection of the rolling bearing type suitable for the application depends on many, different parameters. However, not everything can be calculated in advance. Even if the load and speed are known, additional influencing factors such as temperature, vibration, and the condition of the lubricant must be taken into account. In particular, influencing factors such as contamination can significantly reduce the service life of a rolling bearing and can only be assessed more accurately by means of extensive empirical values.
The following factors are required for the correct design and dimensioning of rolling bearings:
- radial force
- axial force
- direction of load
- speeds / velocity
- temperature
- target life
- deflection and misalignment of the shaft or axis
- Humidity
- Degree of contamination
- Vibrations
- Application-specific requirements
- Environmental influences
- Special installation situation
When dimensioning rolling bearings, a distinction is made, Whether the bearings are loaded dynamically or statically. Recirculating rolling bearings are subjected to dynamic loads. Static load is present when the bearings only perform swivel movements of less than 180°, or are subjected to stationary load. The static load carrying capacity of a rolling bearing is higher than the dynamic load carrying capacity.
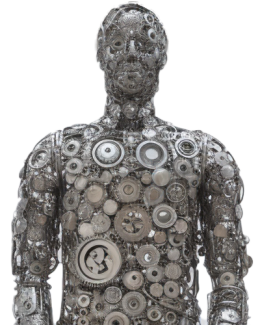
Your contact person
-
Roller bearings sales
-
+49 (2053) 497 - 36
-
Roler bearings
-
+49 (2053) 497 - 0
-
Opening hoursMo-Do.: 08:00 - 16:00
Fr.: 08:00 - 14:45
-
Delivery timesMo-Do.: 06:00 - 13:30
Fr.: 06:00 - 11:00
oder nach Absprache